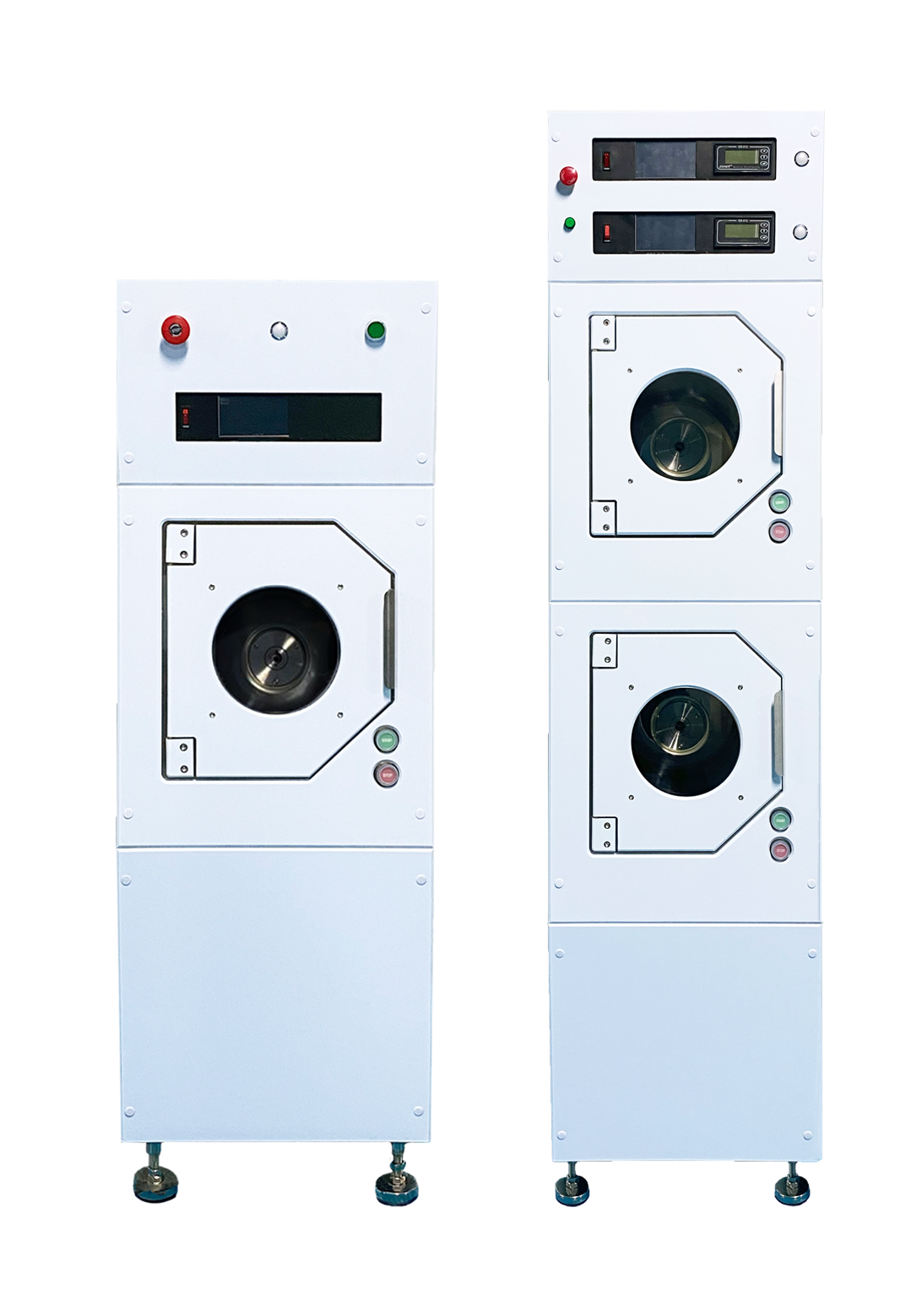
A. Equipment overview
1.1 Applications: Wafer dryer is a high cleanliness washing and drying equipment, with high clean washing, high-speed drying, fast drying, high efficiency characteristics, different wafer sizes, can be quickly replaced by the rotor to achieve. It is the main equipment of wet cleaning process, and the equipment itself has two kinds of structures, single chamber and double chamber, small size and stable operation. It is mainly used for high cleanliness washing and drying process of 2-8 inch semiconductor wafers, mask plates, various substrates and other materials.
1.2 Name: Double chamber dryer
1.3 Model: CSM870S
1.4 Size: 710mm*460mm*1850mm
1.5 Wafer size: 2-6 inches
B. Main structural features
2.1 Structural Features
Double chamber drying machine is mainly composed of spindle drive part, box fixture, working chamber, frame, door cover part, clean pipeline part, electrical control and so on.
2.1.1 Material: Stainless steel frame +10mm PP plate shell
2.1.2 Equipment frame: SUS304 stainless steel material, can meet the working environment of clean room.
2.1.3 The cavity and carrier are made of corrosion-resistant SUS316L stainless steel and electrochemically polished. The carrier can be easily replaced.
2.1.4 The motor and rotor are treated by precise dynamic balance to reduce the resonance of the equipment.
2.1.5 Special custom brushless motor and controller are adopted to ensure the stability and reliability of the equipment and meet the requirements of the system for cleanliness treatment.
2.1.6 Pipe System: PFA clean pipes
2.2 Process cavity and carrier
2.2.1 Number of process cavities: 2 materials are stainless steel 316L (electrolytic polishing of cavity)
2.2.2 Specifications: Processing size 2-6 inches full height box, compatible.
2.2.3 Working speed: 200-2200 RPM/MIN
2.2.4 Heating function: nitrogen heating chamber heating
2.2.5 Shaft seal: Nitrogen shaft seal is used for motor rotation shaft.
2.3 Pure water control unit:
2.3.1 Fan washing nozzle is adopted.
2.3.2 Install a resistivity probe at the drain port to monitor the drainage quality of the cavity.
2.3.3 After the flushing process is complete, nitrogen will blow the deionized water remaining in the flushing pipe.
2.3.4 In standby mode, keep water flowing into the return water box and the flow rate is adjustable.
2.4 Nitrogen control unit:
2.4.1 Pipe fitting valves: SMC solenoid valve, PFA high purity pipe fitting, PTFE air control valve.
2.4.2 Nitrogen heating function: 316 stainless steel heater online heating, temperature switch control, heating temperature control at 80℃.
2.4.3 Equipped with high clean pressure reducing valve, built-in nitrogen filter, filtering accuracy 0.003μm.
2.5 ESD Control Unit:
2.5.1 It consists of a high-pressure generator, a nitrogen ionization chamber and a nitrogen control channel.
2.5.2 When nitrogen passes through the control area of the high-pressure generator, nitrogen ionization fills the entire process chamber, forming a neutral balance to eliminate static electricity.
2.6 Granularity:
Particle added value: need to confirm with the customer
2.7 Electronic Control Unit and software system:
2.7.1 The drying process is controlled by PLC controller + touch screen. You can choose to set a variety of user process menus, and set the contents of each menu such as: time and speed parameters.
2.7.2 The system software also has password permission setting, fault display and alarm functions. When the equipment fails, the system will stop working and display error messages, alarms to prompt changes and repairs.
C. Main technical parameters
Project | Main performance indicators and parameters |
Processing wafer size | 2-6 inch discs |
Quantity of drying per session | 50 |
Number of stations (units) | 2 |
Fragmentation rate | ≤0.01% |
Particle increment | According to customer environment and product requirements |
Rotational speed RPM/MIN | 200-2000 |
Time for drying | 5-8min |
Chamber and nitrogen heating method | Electric heater |
nitrogen gas pressure | 0.25-0.3Mpa,Nitrogen pipe connector3/8” |
Nitrogen consumption L/min | 80 |
Pure water pressure | 0.25-0.3Mpa, pipe 3/8” |
Diain-pipe | 40mmRound pipe PVC pipe |
Control system | Mitsubishi PLC programmable controller |
Display | 4.3-inch touch screen |
Power supply | AC220V |
Machine power | 5 KW |
Dimensions (D * W * H) mm | 710mm*460mm*1850mm |